100 years of CUI management
CUI is a form of corrosion that occurs in insulated piping when moisture intrudes the insulation and is absorbed. This is a central issue within all industries that utilise insulated piping made of carbon, stainless steel and low alloy steel. Industries such as chemical, petrochemical, refining, marine and offshore industries are prevalent to this issue and damages caused by CUI can result in both financial and environmental damages that are irreparable.
For more than 100 years the approach to CUI monitoring has been to manually dismantle cladding from piping in order to assess its condition. In the later years this approach has been tweaked slightly to become a risk based inspection (RBI). A risk based inspection also requires the insulated piping to have its cladding dismantled, but on a much smaller scale. Predictive data modelling is applied to determine which areas are most prone to CUI, and thus should be inspected.
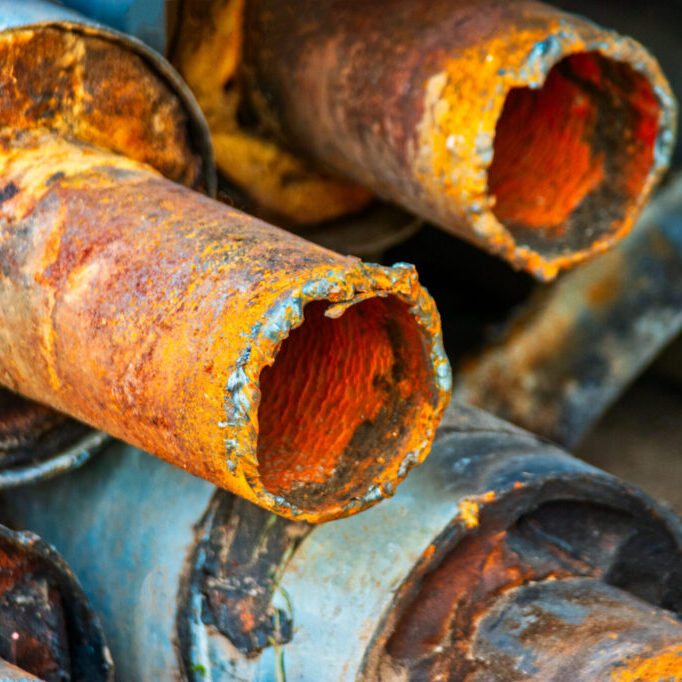
Drawbacks and advantages of the RBI model
The advantage of an RBI compared to the traditional approach is that it will lead to less waste since less cladding is being removed from the piping. The drawback is that there is more room for false negatives, i.e. areas of the piping that previously have been deemed safe against CUI but for various reasons have developed corrosion regardless. Another drawback is that a lot of false positives still occur, with cladding being removed prematurely, leading to huge amounts of waste in the form of old cladding.
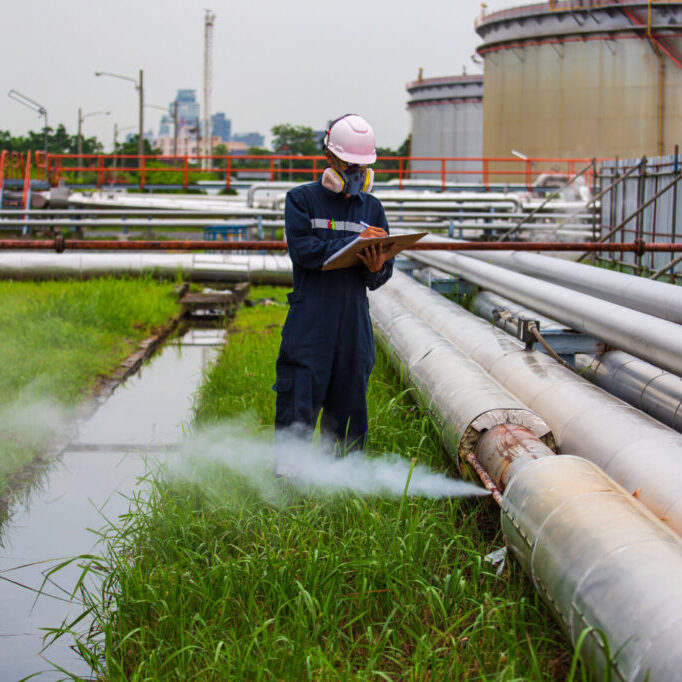
Why the RBI model is failing to manage CUI
The status quo of CUI management is much the same as it was decades ago. With minor tweaks having been made to the process in an effort to make it more streamlined, companies are still collectively spending trillions of dollars battling corrosion each year. Even though some statistical analysis is utilized as part of the RBI model, there are still massive drawbacks that make this approach flawed. The common denominator for these flaws: Costs. Costs to the bottom line as well as costs to the environment.
Costly to the bottom line
When removing cladding and insulation to perform inspections in a traditional CUI approach, approximately 90% of the inspected areas turn out to have dry insulation and intact coating. Hence, there are substantial cost saving opportunities by applying a data driven approach to prioritize inspections based on actual water exposure.
Costly to the environment
There are two ways in which the conventional risk based approach is costly to the environment: First, in order to inspect the piping for corrosion, the piping’s cladding has to be removed. Even just to find no corrosion, a false positive, the cladding has to be removed. With the current ratio of false positives being as high as 90%, this leads to enormous volumes of waste being disposed of. Even disregarding the environmental cost of trying to recycle this cladding, the environmental costs of producing the cladding to begin with are massive.
Second, a figure that is rarely talked about is the false negatives a risk based inspection approach brings with it. Nearly all CUI related major incidents are caused by false negatives. A false negative in the case of risk based inspection is when CUI occurs in a section of piping that was not deemed prone to have CUI risk and thus was never inspected.
The future of predictive CUI monitoring
CirruSense is a complete, cloud-based, ecosystem for gathering, structuring, analyzing and visualizing data from your plant's sensors and assets. It gives you a 24/7 overview of your plant’s status from virtually anywhere in the world. With CirruSense Monitoring-as-a-Service you can achieve significant cost savings on your CUI maintenance, increase your plant's technical integrity and become a more sustainable business.